In the intricate world of modern technology, rare earth magnets have emerged as unsung heroes, powering everything from wind turbines and electric vehicles to smartphones and hard – disk drives. Their exceptional magnetic properties, such as high magnetic strength and coercivity, make them indispensable in countless applications. But what exactly are these remarkable magnets made from? The answer lies in a combination of rare earth elements and other materials, carefully engineered to create a powerful magnetic force.
Rare Earth Elements: The Core Ingredients
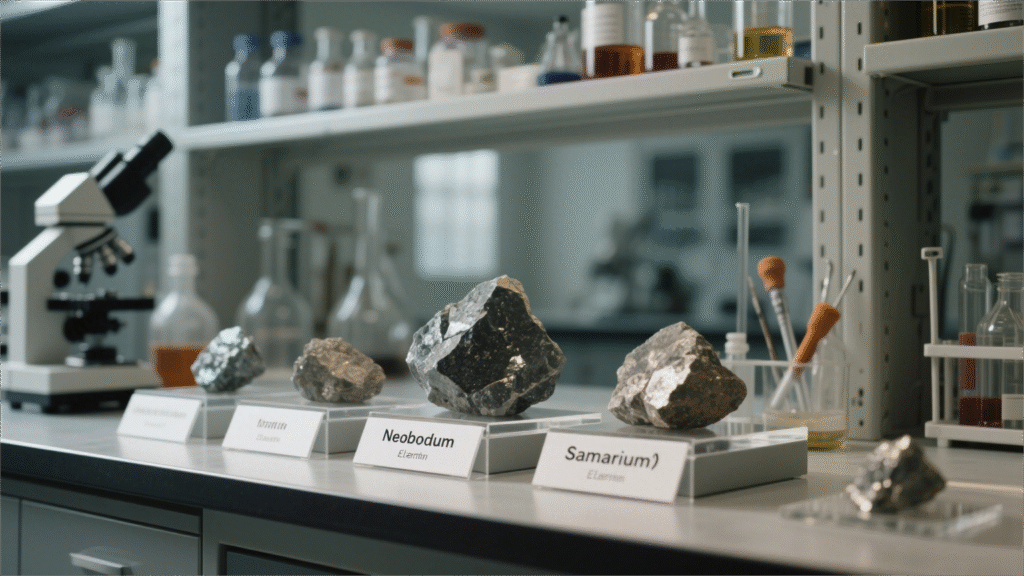
- Iron (Fe): As mentioned earlier, iron is a key component of NdFeB magnets. It provides the magnetic structure and contributes to the overall strength of the magnet.
- Boron (B): Boron is added to NdFeB magnets to stabilize the crystal structure and enhance the magnet’s performance. It helps to prevent the formation of unwanted phases and improves the magnetic properties of the magnet.
- Cobalt (Co): Cobalt is used in SmCo magnets to improve their temperature stability and magnetic properties. It also helps to increase the coercivity of the magnet, making it more resistant to demagnetization.
- Aluminum (Al): Aluminum is sometimes added to NdFeB magnets to improve their corrosion resistance and mechanical properties. It can also help to reduce the cost of the magnet by replacing some of the more expensive rare earth elements.
- Copper (Cu): Copper is used in some rare earth magnets to improve their electrical conductivity and thermal properties. It can also help to enhance the magnet’s performance by reducing eddy current losses.

The Manufacturing Process
- Mining and Refining: The first step in the production of rare earth magnets is the mining and refining of rare earth elements. Rare earth minerals are typically found in deposits around the world, and the mining process involves extracting the minerals from the ground and separating them into their individual elements. The refining process then purifies the rare earth elements to remove any impurities and prepare them for use in magnet production.
- Alloying: Once the rare earth elements have been refined, they are combined with other materials, such as iron, boron, and cobalt, to form an alloy. The alloy is then melted and cast into ingots or billets, which are used as the raw material for magnet production.
- Milling and Powdering: The ingots or billets are then milled and powdered to create a fine powder. The powder is typically less than 10 micrometers in size and has a uniform particle size distribution.
- Magnetization and Sintering: The powder is then compacted into the desired shape using a process called isostatic pressing. The compacted powder is then magnetized using a strong magnetic field and sintered at high temperatures to densify the powder and improve the magnetic properties of the magnet.
- Machining and Finishing: After sintering, the magnets are machined and finished to the desired shape and size. This may involve cutting, grinding, drilling, and polishing the magnets to achieve the required surface finish and dimensional accuracy.
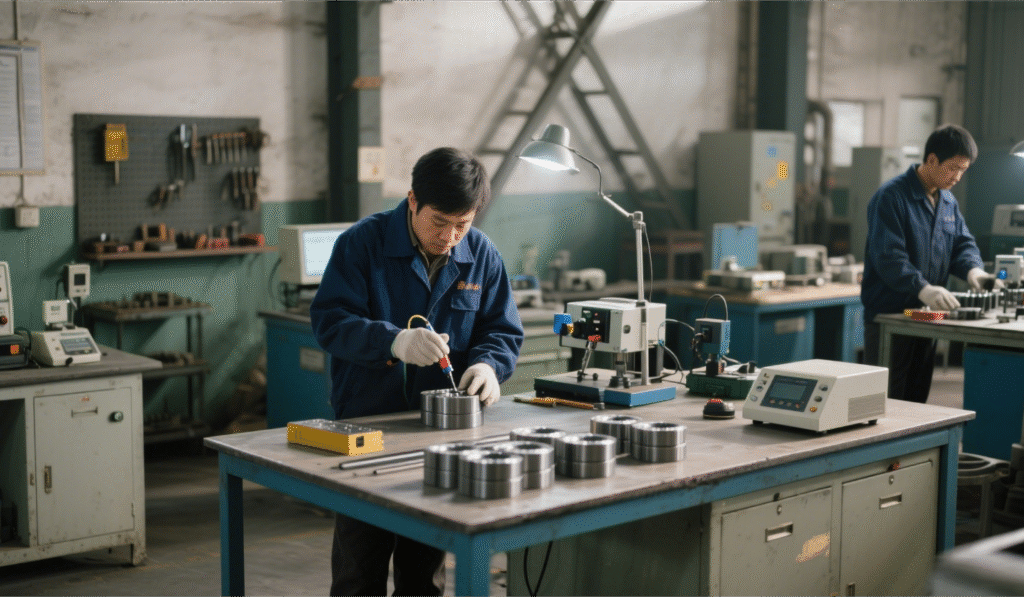
The Importance of Rare Earth Magnets
- Electric Vehicles and Renewable Energy: Rare earth magnets are used in the electric motors and generators of electric vehicles and renewable energy systems, such as wind turbines and solar panels. Their high magnetic strength and efficiency make them ideal for these applications, as they help to reduce energy consumption and increase the performance of the vehicles and systems.
- Consumer Electronics: Rare earth magnets are also used in a variety of consumer electronics products, such as smartphones, laptops, tablets, and headphones. They are used in the speakers, microphones, and hard – disk drives of these products, as well as in the vibration motors and magnetic sensors.
- Medical Devices: Rare earth magnets are used in a number of medical devices, such as MRI machines, pacemakers, and insulin pumps. Their high magnetic strength and precision make them ideal for these applications, as they help to improve the accuracy and effectiveness of the medical devices.
- Aerospace and Defense: Rare earth magnets are used in a variety of aerospace and defense applications, such as aircraft engines, missile guidance systems, and radar systems. Their high magnetic strength and reliability make them essential for these applications, as they help to ensure the safety and performance of the aircraft and weapons systems.
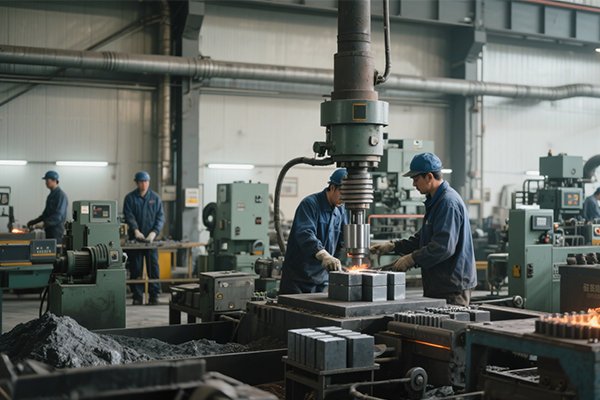
Conclusion
Rare earth magnets are primarily made from neodymium-iron-boron (NdFeB) or samarium-cobalt (SmCo) alloys. Their incredible strength and durability make them indispensable in modern technology. However, because rare earth elements are challenging to mine and refine, researchers are continually exploring alternative materials to reduce reliance on them.
Would you like more details on how these magnets are manufactured or their environmental impact? Let me know!