Description
Magsafe Wireless Charger Dedicated Neodymium Magnets
Factory Strength: An Industry Benchmark Controlling Quality from the Source
As a professional manufacturer with years of expertise in rare earth permanent magnets, we possess:
- Thousands of square meters of modern production bases: Equipped with fully automatic neodymium iron boron molding equipment, high-precision cutting machines, and surface treatment production lines, with an annual capacity of over 1 million pieces. We support independent production from raw material smelting to finished product inspection.
- Senior technical team: Bringing together engineers in materials science and magnetism fields, we can quickly complete magnetic circuit design, tolerance optimization, and special performance debugging (such as high temperature resistance, corrosion resistance, etc.) as required by customers. We have provided customized magnet solutions for more than 300 consumer electronics brands worldwide.
- International certification system: Certified by ISO9001 quality management system and RoHS/REACH environmental protection standards, ensuring that products comply with global market standards from materials to processes.
Core Product Advantages: The Perfect Combination of High Precision and Customization
Parameter Dimension | Technical Highlights | Customization Options |
---|---|---|
Shape | Ring structure design, suitable for precise alignment with Magsafe wireless charger magnetic modules | Customizable special-shaped structures (such as arcs, sectors, multi-pole combinations, etc.) |
Precision | Tolerance controlled at ±0.05mm, fully inspected by a coordinate measuring machine to ensure the gap error with the charging coil is <0.1mm | Support ultra-high precision customization with a tolerance of ±0.03mm (advance communication required) |
Magnetic Performance | Made of N52 grade strong neodymium iron boron materials, remanence ≥14.8kGs, magnetic energy product up to 52MGOe | Various grades from N35 to N55 are available as needed, or alternative materials such as samarium cobalt and ferrite |
Surface Treatment | Standard NiCuNi three-layer electroplating, salt spray test ≥72 hours without rust | Optional special processes such as epoxy resin encapsulation, rubber coating, gold/zinc plating, etc. (to meet waterproof and scratch-resistant requirements) |
Magnetization Direction | Support radial, axial, and thickness direction magnetization, magnetic flux uniformity ≥95% | Customizable multi-pole magnetization (such as 4-pole, 8-pole) to adapt to complex magnetic circuit designs |
Environmental Adaptability | Conventional temperature resistance of 100℃, special processes can reach 230℃ (such as aerospace-grade high-temperature coatings) | Customizable models for wide temperature environments from -40℃ to 230℃, accompanied by temperature decay test reports |
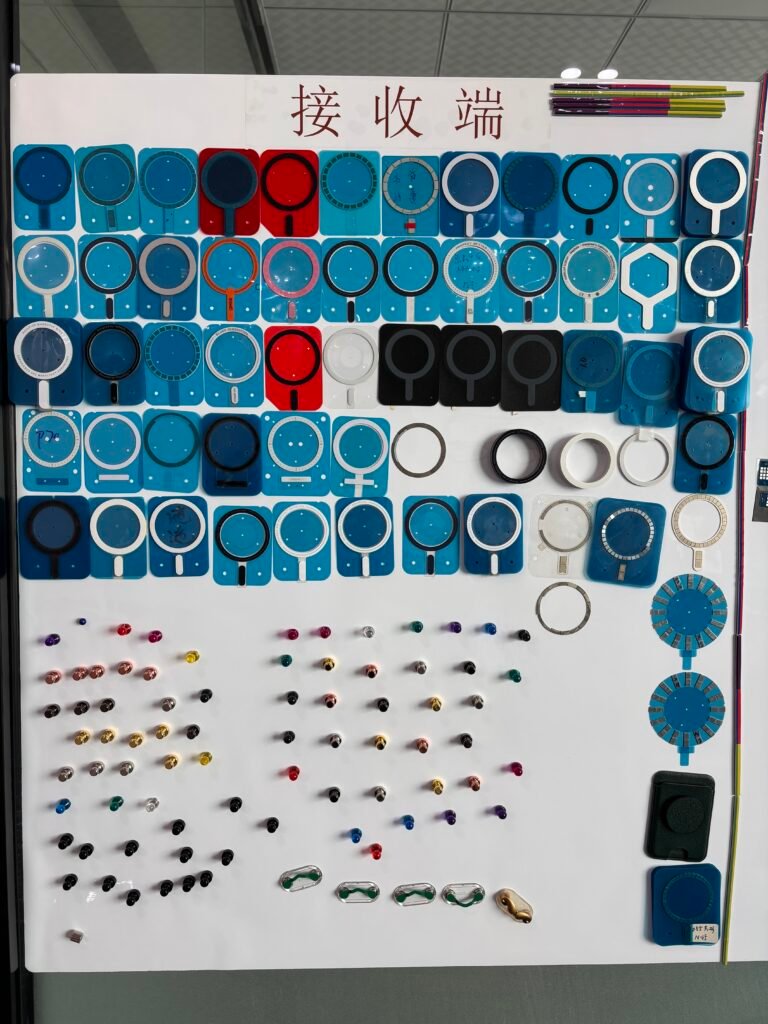
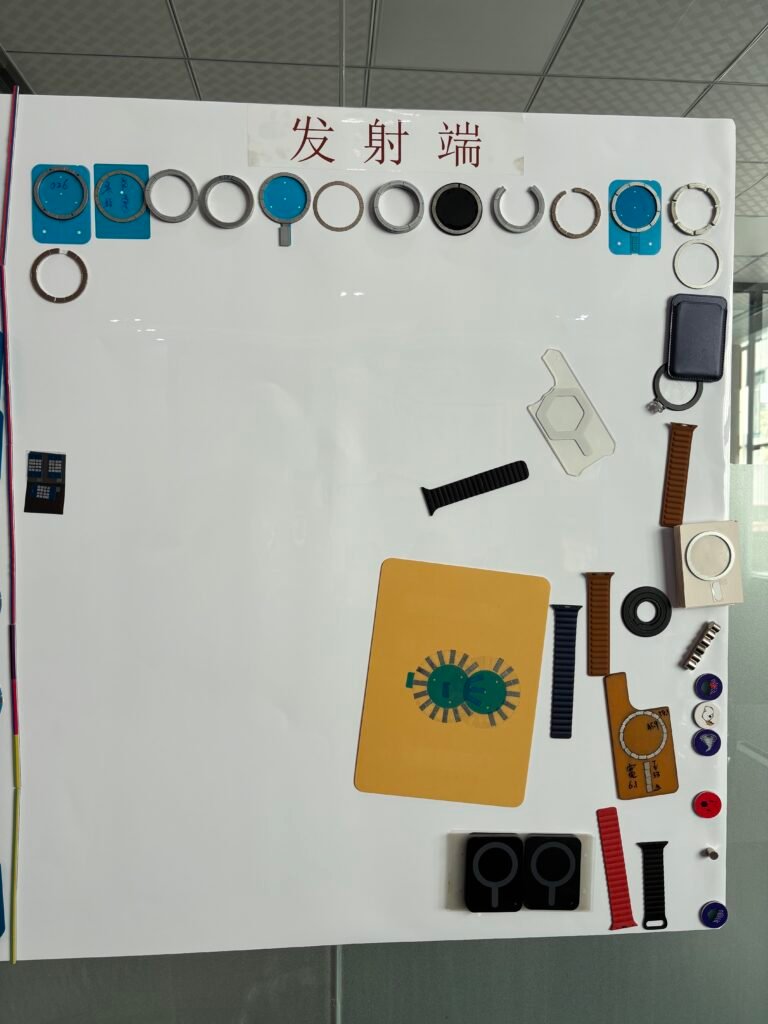
Quality Assurance: A Full-Process Testing System Ensuring Safety
- Raw Material Control: Each batch of rare earth raw materials is tested by a spectrometer to ensure that the content of elements such as neodymium and boron meets the standards, rejecting recycled material doping.
- Process Monitoring: Real-time monitoring of magnetic field distribution, dimensional accuracy, and coating adhesion during production. AI visual inspection equipment is set up for key processes, with the defect rate controlled below 0.3%.
- Finished Product Testing:
- Magnetic performance testing: Use gauss meters and hysteresis loop testers to ensure that parameters such as magnetic induction intensity and coercive force meet the standards;
- Environmental testing: Verify weather resistance through high and low-temperature alternating test chambers and damp heat test chambers, simulating extreme use scenarios;
- Reliability testing: Drop test (1.5m free fall), vibration test (frequency 20-2000Hz) to ensure no magnetic damage during transportation and use.
Customization Services: One-Stop Response from Requirement to Delivery
- Flexible minimum order quantity: Free Samples,Support small-batch sampling (starting from 1 pieces), sample delivery within 3 days, and mass production cycle of 3-5 days.
- Exclusive solution design: Provide free magnetic circuit simulation design services, and optimize magnet specifications according to customers’ charger power and size requirements (such as the currently 54*4mm ring, thickness can be adjusted from 2-10mm).
- Global service network: Equipped with a professional foreign trade team, supporting English and Japanese technical docking, providing various delivery methods such as DDP/FOB, and responding to quality feedback within 24 hours after-sales.
Cooperation Cases: Empowering Magnetic Innovation for Global Brands
- Customized 150℃ high-temperature resistant radially magnetized ring magnets for a North American 3C accessories brand, suitable for high-temperature environments of vehicle-mounted wireless chargers, with an annual purchase volume of over 100,0000 pieces;
- Designed multi-pole magnetized magnetic modules for a European smart home manufacturer, with a magnetic force error <2%, helping it achieve the “blind magnetic attraction” function of charging bases.
FAQ
Q1: Can your ring-shaped neodymium magnets fit Magsafe wireless chargers from different brands?
A: Our ring magnets are designed with standardized precision (tolerance controlled at ±0.05mm), compatible with magnetic modules of mainstream Magsafe chargers on the market. For customization, simply provide your specific dimensions and magnetization direction requirements—our technical team will optimize the design to ensure perfect fit.
A: Our ring magnets are designed with standardized precision (tolerance controlled at ±0.05mm), compatible with magnetic modules of mainstream Magsafe chargers on the market. For customization, simply provide your specific dimensions and magnetization direction requirements—our technical team will optimize the design to ensure perfect fit.
Q2: What is the temperature resistance of the product? Can it withstand high temperatures in vehicle-mounted environments?
A: Standard models resist up to 100℃, while special processes enable heat resistance up to 230℃. For vehicle applications, we’ve customized radially magnetized ring magnets with 150℃ resistance for North American clients, which passed strict high-low temperature cycling tests to ensure stable performance.
A: Standard models resist up to 100℃, while special processes enable heat resistance up to 230℃. For vehicle applications, we’ve customized radially magnetized ring magnets with 150℃ resistance for North American clients, which passed strict high-low temperature cycling tests to ensure stable performance.
Q3: What is the minimum order quantity (MOQ)? How long does sampling and mass production take?
A: We support low MOQ sampling starting from 1 pieces, with a 2-day sample lead time. Mass production typically takes 3-5 days, ensuring quick response to your needs.
A: We support low MOQ sampling starting from 1 pieces, with a 2-day sample lead time. Mass production typically takes 3-5 days, ensuring quick response to your needs.
Q4: How do you ensure long-term stability of magnetic performance?
A: We implement full-process quality control: raw materials are tested for purity via spectrometers; magnetic field distribution is monitored in real-time during production; finished products undergo magnetic performance tests (using gauss meters and hysteresis loop testers) and reliability tests (drop, vibration, etc.). All products comply with ISO9001 and come with complete inspection reports.
A: We implement full-process quality control: raw materials are tested for purity via spectrometers; magnetic field distribution is monitored in real-time during production; finished products undergo magnetic performance tests (using gauss meters and hysteresis loop testers) and reliability tests (drop, vibration, etc.). All products comply with ISO9001 and come with complete inspection reports.
Q5: Besides NiCuNi plating, what other surface treatment options are available?
A: In addition to standard NiCuNi triple-layer plating (salt spray test ≥72 hours), we offer epoxy encapsulation, rubber coating, gold plating, zinc plating, and more—tailored to waterproof, scratch-resistant, or anti-corrosion requirements for different scenarios.
A: In addition to standard NiCuNi triple-layer plating (salt spray test ≥72 hours), we offer epoxy encapsulation, rubber coating, gold plating, zinc plating, and more—tailored to waterproof, scratch-resistant, or anti-corrosion requirements for different scenarios.
If you are interested in Magsafe magnet products or have custom requirements, please send an email and I will reply you as soon as possible. Free samples are available!
There are no reviews yet.