Neodymium magnets do rust. I see this happen because they contain a lot of iron, which reacts easily with moisture and air. Most neodymium magnets have a shiny coating to protect them, but these coatings can chip or wear out over time. > I always pay attention to rust because it can weaken the magnet and shorten its life.
- Neodymium magnets can rust because they have iron. Iron reacts fast with water and air. Coatings like nickel-copper-nickel and epoxy help protect magnets. But these coatings can wear out or chip as time passes. High humidity, water, salt, chemicals, and temperature changes make rust form faster. Check magnets often for chips, cracks, rust spots, or if they feel weaker. Keep magnets in dry, closed containers with silica gel packs. This helps lower moisture and stops rust. Be gentle when handling magnets to keep the coating safe. Damaged coatings can let rust start. If you see rust, clean it soon with gentle cleaners or rust removers. After cleaning, protect the magnet again. If rust is deep, flakes off, or makes the magnet weak, replace it. This keeps your projects safe.
Why Rust Happens
Iron Content
Neodymium magnets are made from neodymium, iron, and boron. Iron is the biggest part of the magnet. This is why these magnets rust so fast. Iron reacts with water and air very quickly. Making the magnet does not stop the iron from rusting. Tests show magnetized neodymium magnets rust faster than non-magnetized ones. The magnetic field pulls oxygen closer to the magnet. This makes rust form even faster. I have seen that iron in these magnets reacts with moisture. This happens a lot in wet places.
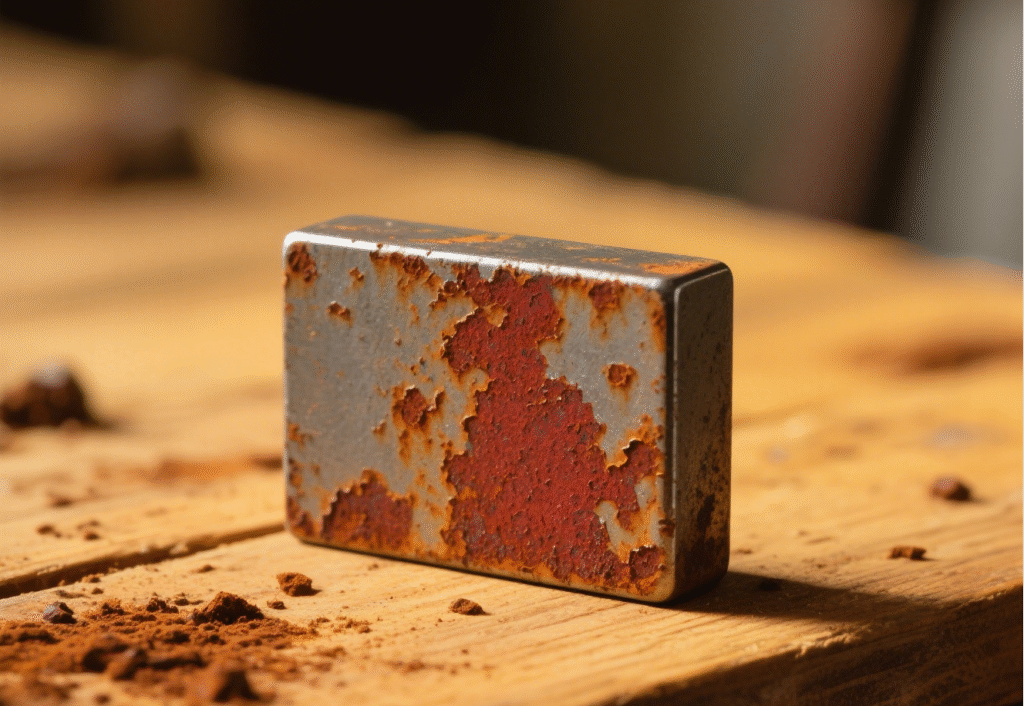
Corrosion Process
Rust starts on the outside of the magnet. It can go deeper if the coating breaks. The magnet is cleaned and treated before getting a coating. These steps use grinding, chemicals, and weak acids to clean it. Then, the magnet gets a nickel or zinc coating. If the coating cracks, water and air get inside. Neodymium-rich parts rust even faster than iron. This makes the rust worse. I have seen rust spread inside the magnet. The surface flakes off and the magnet gets weaker. Adding metals like aluminum or chromium can slow rust. But coatings are still the best protection. In salty or wet air, rust can show up in a week. The magnet can lose up to 11% of its strength.
Coating Role
Coatings help keep neodymium magnets safe from rust. I always look for nickel, copper, or epoxy coatings. These coatings block water and air from the iron. Tests show epoxy coatings last longest in water. They can last up to seven weeks. Even the best coatings can break if scratched. When this happens, rust starts fast and the magnet gets weak. Using more than one coating, like nickel and epoxy, works better in wet or salty places. Coatings help the magnet last longer and stay strong. But no coating can stop rust forever. I always handle magnets carefully and check for damage.
Tip: Always look for chips or cracks in the coating. Even a tiny scratch can let water in and start rust.
Neodymium Magnets and Rust
Susceptibility
Neodymium magnets can rust faster than you might think. The iron inside reacts quickly with water and air. Even a tiny scratch can let rust start. The shape of the magnet also matters. Some shapes, like bread-loaf or laminated, are hard to cover fully. This makes some parts more likely to rust. I always check the corners and edges first. These spots usually show rust before other areas.
Here is a table that shows how different coatings protect magnets in tough conditions:
Parameter | Everlube Coating (Control) | Black Epoxy Coating (Test) |
---|---|---|
Salt Spray Exposure | 5% NaCl at 35°C, continuous spray | 5% NaCl at 35°C, continuous spray |
Duration | Up to 72 hours (rust visible by 24-48 hours) | Up to 408 hours (17 days), rust only in small spots at edges/corners |
Rust Coverage | Significant rust within 24 hours; none passed after 48 hours | Rust spots appeared after 48-72 hours; rust coverage <10% surface area even after 17 days |
Mass Loss (range) | N/A | 0.07g to 0.78g (0.173% to 1.924%), average 0.907% |
Magnetic Moment Loss (range) | N/A | 0.041% to 0.453%, average 0.216% |
Magnet Design | Bread-loaf shape, laminated magnets | Bread-loaf shape, laminated magnets |
Coating Challenges | N/A | Laminated design limits Ni-Cu-Ni finish; epoxy applied thickly but thinner at edges/lamination lines |
Conclusion | Poor corrosion resistance | Epoxy coating provides strong corrosion protection, maintaining magnet performance over extended exposure |
This table shows that black epoxy coatings work much better than Everlube. After 17 days in salty spray, epoxy-coated magnets only had a few small rust spots at the edges.
Unplated Magnets
I never use neodymium magnets without a coating in wet places. If there is no coating, the iron reacts with water and air right away. I have seen uncoated magnets start to rust in just a few hours. The rust makes the magnet weak and can break it apart. I always tell people not to use uncoated magnets unless they stay dry. Even a little water in the air can make them rust.
Note: Unplated magnets lose their strength and shape much faster than coated ones. Always choose a coated magnet for any project that might get wet.
Surface vs. Internal Rust
Surface rust starts when water or air touches the outside. This happens if the coating gets scratched or chipped. The rust looks like brown or orange spots on the magnet. If I do not fix it, the rust can go deeper inside. Internal rust is worse than surface rust. It can break the magnet from the inside out. Sometimes, the outside still looks fine, but the inside is already falling apart. Laminated designs are hard to coat on every layer. This lets rust start between layers where you cannot see it.
I always check my magnets for rust on the surface and at the edges. If I see any damage, I replace the magnet right away. This helps me stop bigger problems later.
Environmental Factors
Humidity
Humidity plays a huge role in how fast neodymium magnets rust. I have seen magnets left in damp air start to show rust spots much faster than those kept dry. When the air holds a lot of moisture, water vapor lands on the magnet’s surface. This moisture lets electrochemical reactions start, which leads to rust. Scientists use special tests, like the 85/85 test, where they put magnets in 85% humidity at 85°C. In these tests, magnets rust and break down much faster than in dry air. Even without exact numbers, I know that high humidity always speeds up rust. If you live near the ocean or in a rainy place, you need to be extra careful. I always store my magnets in dry, sealed containers to keep moisture away.
Tip: Use silica gel packs in storage boxes to absorb extra moisture and protect your magnets from humidity.
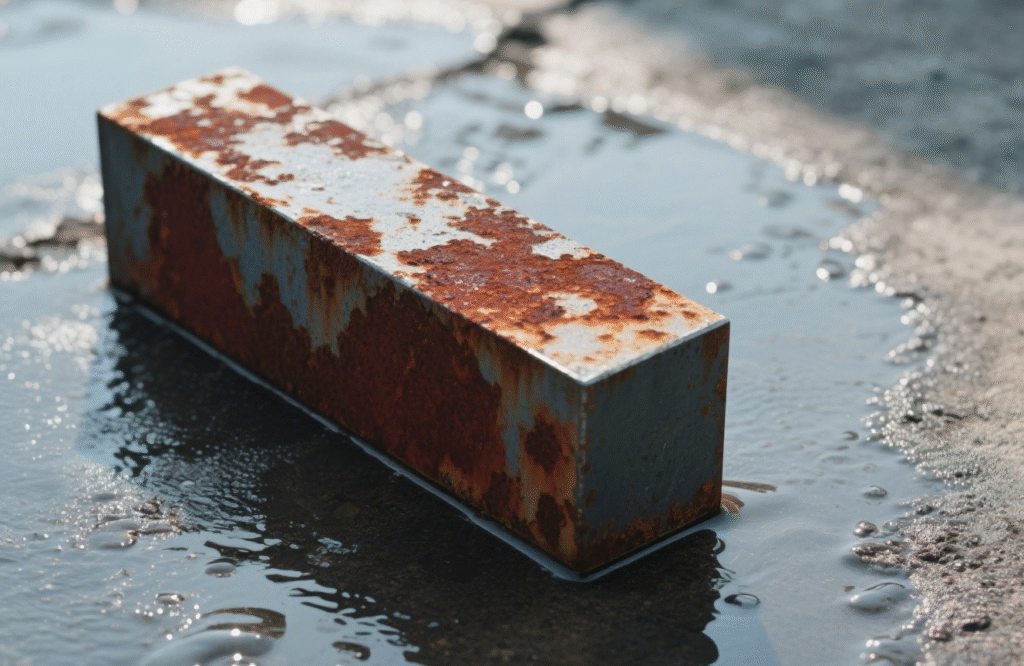
Water Exposure
Direct contact with water is even worse for neodymium magnets. I once dropped a coated magnet in a puddle. After just a few hours, I saw tiny rust spots where the coating had chipped. Water seeps into cracks and scratches, reaching the iron inside. Once water gets in, rust forms quickly and spreads. Even a short splash or spill can start the process. If you use magnets outdoors or in wet places, you need to check them often. I always dry my magnets right away if they get wet. For projects near water, I use magnets with extra-strong epoxy coatings or seal them in waterproof cases.
- Always dry magnets after cleaning.
- Avoid using uncoated magnets near water.
- Check for chips or cracks before using magnets in damp places.
Salt and Chemicals
Salt and chemicals make rust form even faster. I learned this the hard way when I used magnets near the ocean. Salt in the air or water acts as a catalyst, speeding up the corrosion process. Scientific studies show that saltwater can double or even triple the corrosion rate of iron-based materials. In one test, pure iron in a salt solution rusted twice as fast as normal. Iron-manganese alloys rusted almost three times faster. The table below shows how salt affects corrosion rates:
Material | Test Duration | Environment | Corrosion Rate Change |
---|---|---|---|
Pure Iron (Fe) | 14 days | Salt solution | Corrosion rate doubled |
Iron-Manganese Alloy | 14 days | Salt solution | Corrosion rate nearly tripled |
Chemicals like acids or cleaning agents can also damage the coating and expose the iron. I always keep magnets away from salty air, cleaning sprays, and harsh chemicals. If you must use magnets in these places, pick ones with thick, high-quality coatings and check them often for damage.
Temperature Changes
Temperature changes can make neodymium magnets rust faster. I have seen this happen many times, especially when magnets move from a cold place to a warm, humid one. When the temperature goes up and down, water in the air can turn into tiny droplets on the magnet’s surface. This is called condensation. Condensation gives water a way to reach the iron inside the magnet. Once water touches the iron, rust starts to form.
I remember one winter when I stored magnets in my garage. The temperature dropped at night and rose during the day. Every morning, I found a thin layer of moisture on the magnets. After a few days, I saw small rust spots appear, even though the magnets had a coating. The coating did not stop the water from getting in through tiny cracks. This taught me that temperature swings can be just as bad as direct water contact.
Here is what happens when temperature changes affect magnets:
- Warm air holds more moisture than cold air.
- When warm, moist air touches a cold magnet, water forms on the surface.
- Water finds its way into small scratches or chips in the coating.
- Rust starts to grow where water meets iron.
Tip: Always let magnets warm up to room temperature before opening sealed containers. This helps stop condensation from forming on the surface.
I also learned that sudden temperature changes can damage the coating itself. Some coatings, like epoxy, can crack if the magnet heats up or cools down too quickly. Cracks let water and air reach the iron inside. Once the coating breaks, rust spreads much faster.
I use a few simple steps to protect my magnets from temperature changes:
- Store magnets in a place with steady temperature.
- Avoid moving magnets from cold to warm rooms too quickly.
- Keep magnets in airtight containers to block moist air.
- Use silica gel packs to absorb extra moisture.
I check my magnets often, especially after big temperature swings. If I see any signs of rust or damage, I clean or replace the magnet right away. I learned that prevention works better than trying to fix rust later.
Temperature changes may seem harmless, but they can cause big problems for neodymium magnets. By keeping magnets dry and avoiding sudden temperature shifts, I help them last longer and stay strong.
Coatings for Neodymium Magnets
Nickel-Copper-Nickel
Most neodymium magnets I buy have a nickel-copper-nickel coating. This coating has three layers and looks shiny and silver. The first nickel layer sticks to the magnet and helps stop rust. The copper layer adds more protection. The last nickel layer makes the surface hard and smooth. I like this coating because it works in many places. It keeps the magnet safe from scratches and light moisture. If I keep these magnets dry and handle them gently, they last a long time.
I read some studies about how long this coating lasts. In high humidity at 60°C, nickel-coated magnets can resist rust for over 2,500 hours before the coating fails. In salt spray tests, they last more than 48 hours. I use these magnets in electronics, tools, and some medical devices. The hard surface also makes them easy to clean.
Other Coatings
Sometimes, I need special coatings for different jobs. Here are some other options I have used:
- Zinc: Good for outdoor use. It resists rust and costs less than nickel.
- Gold: Great for medical devices. It resists corrosion and is safe for the body.
- Silver: Works well in electronics. It conducts electricity and resists rust.
- Rubber: Adds grip and protects against impact. I use these in cars and machines.
- PTFE (Teflon): Handles chemicals and high heat. I pick this for lab work.
- Parylene: Makes a thin, even layer. It blocks moisture and chemicals, so I use it in electronics and medical tools.
I always pick the coating that fits the job. Each type has good and bad points. The right coating helps neodymium magnets last longer and work better in tough places.
Coating Type | Best Use Cases | Key Features |
---|---|---|
Nickel-Copper-Nickel | Electronics, tools, medical | Hard, shiny, strong against wear |
Epoxy | Outdoors, humid, chemicals | Thick, blocks moisture, many colors |
Zinc | Marine, outdoor | Cost-effective, rust resistant |
Gold | Medical, high corrosion | Biocompatible, top corrosion proof |
Silver | Electronics | Conductive, rust resistant |
Rubber | Automotive, industrial | Impact and water resistant |
PTFE | Chemical, high temp | Chemical proof, low friction |
Parylene | Medical, electronics | Thin, even, strong barrier |
Tip: Always check the coating before you use a magnet. Even a small chip can let water in and start rust.
Coating Effectiveness
Here is a table that compares different coatings:
Coating Type | Protective Properties | Best Use Cases | Advantages / Limitations |
---|---|---|---|
Nickel-Copper-Nickel | Good corrosion resistance, shiny finish | Everyday, dry environments | Durable, common, not for harsh moisture |
Zinc | Moderate corrosion resistance, stable to 80°C | Outdoor, moderate moisture | Cost-effective, limited by temperature |
Epoxy | Excellent corrosion resistance, thick layer | Wet, outdoor, harsh chemicals | Great for water, can chip if dropped |
Gold | High corrosion resistance, conductive | Medical, water, high-end uses | Premium, expensive, very protective |
Parylene | Exceptional corrosion resistance, thin layer | Electronics, harsh environments | Long-lasting, hard to see, costly |
Teflon (PTFE) | Chemical resistance, non-stick | Labs, chemical exposure | Stops chemicals, reduces wear, slippery |
Everlube | Lubrication, wear resistance | Moving parts, machines | Reduces friction, not for water |
Chrome | Good against rubbing and pressure | Spheres, high wear areas | Durable, dull color, not for water |
Copper | Decorative, shiny color | Looks only, not for protection | Wears out fast, not for wet places |
I use nickel-copper-nickel coatings for most projects. They work well in dry rooms and last if not scratched. For outdoor or wet places, I choose epoxy or parylene. Epoxy blocks water better than nickel, but it can chip if dropped. Parylene is thin and clear, and it blocks water and chemicals, but it costs more.
What to Do If Rust Appears
Early Signs
I always look for early signs of rust on my neodymium magnets. Small brown or orange spots often show up first. Sometimes, I notice a rough or flaky surface. The magnet may feel weaker or look dull. I check the corners and edges because rust often starts there. If I see any change in color or texture, I know rust has started. A strange metallic smell can also be a warning sign. I make it a habit to inspect my magnets after every use, especially if they have been near water or in humid air.
Cleaning
When I find rust, I act quickly. Cleaning the magnet right away can save it. I start by rinsing the magnet with warm water and a little dish soap. This removes dirt and loose rust. For light rust, I use a 50/50 mix of water and white vinegar. I soak the magnet for a few minutes, then scrub gently with a soft-bristle brush. This helps me clean without scratching the coating.
If the rust is heavy, I use a rust remover like Naval Jelly or a non-toxic product such as Evapo-Rust. I always wear gloves and work in a well-ventilated area when using chemicals. For tough spots, I pick the right brush. Steel wire brushes work for heavy rust, but I use brass or nylon brushes for softer cleaning. After cleaning, I rinse the magnet with fresh water and dry it completely.
I protect the clean magnet by applying a thin layer of oil, like WD-40 or 3-in-1 oil. This keeps moisture away. Sometimes, I use a rust inhibitor spray or a sealant like Renaissance Wax. These products form a barrier against future rust. I store the magnet in an airtight container with silica gel packs to keep it dry.
Here is my cleaning checklist:
- Rinse with warm water and dish soap.
- Use vinegar or a rust remover for stubborn rust.
- Scrub gently with the right brush.
- Dry the magnet well.
- Apply a light oil or rust inhibitor.
- Store in a dry, sealed box.
Replacement
Sometimes, cleaning does not fix the problem. If the magnet has deep rust, flakes, or cracks, I replace it. A weak or broken magnet can be unsafe. I never use magnets that have lost their coating or have rust inside. Replacement is the safest choice when the magnet feels weak or looks badly damaged.
I choose a new magnet with a strong protective coating. I also review how I store and handle my magnets to prevent rust in the future. Regular inspection and quick action help me keep my magnets strong and safe for a long time.
Rust happens mostly because the iron in the magnet meets water. I use coatings like nickel-copper-nickel or epoxy to help stop rust, but these coatings do not last forever. Storing magnets well and handling them gently helps them last longer. I look for chips or cracks a lot and keep my magnets dry.
- Pick the best coating for your project
- Keep magnets in dry, closed boxes
- Check magnets often
FAQ
Do all neodymium magnets rust the same way?
No, I have seen that magnets with better coatings resist rust longer. Magnets in wet or salty places rust faster. Shape and size also matter. Edges and corners often rust first.
Can I paint over a chipped magnet to stop rust?
Yes, I sometimes use clear nail polish or epoxy to cover small chips. This helps block water and air. It is a quick fix, but not a permanent solution. I always check for new chips.
Are neodymium magnets safe to use outdoors?
I use them outdoors, but only with strong coatings like epoxy or rubber. I always keep them dry and check for damage. Uncoated magnets rust very fast outside.
How do I know if my magnet is losing strength from rust?
I notice the magnet feels weaker or does not stick as well. Sometimes, I see rust spots or flakes. If I spot these signs, I test the magnet’s pull and check for more damage.
Can I store neodymium magnets in the fridge or freezer?
I avoid storing magnets in the fridge or freezer. Cold air can cause condensation when I take them out. This moisture can start rust. I keep magnets in a dry, room-temperature place.
What should I do if my magnet gets wet?
I dry it right away with a soft cloth. I check for chips or cracks. If I see any, I cover them or replace the magnet. I store it in a dry box with silica gel packs.
Do stronger magnets rust faster than weaker ones?
Yes, I have noticed that stronger magnets can rust faster. Their magnetic field pulls in more moisture and oxygen. This speeds up rust, especially if the coating is damaged.
Tip: Always inspect your magnets after use, especially if they have been near water or in humid air.